Spray fémezés
Ezek az anyagok használhatók formájában huzal (gömbgrafitos fémek), porok (rideg fémek, fém-oxidok, műanyagok), rudak nyert zsugorított (fém-oxidok), vagy paszták (műanyag). A leggyakrabban használt anyagok és azok jellemzőit mutatjuk be (a teljes listát nem lehetséges, mert a gyártók gyakran módosítják őket). Ezenkívül a hegesztési huzal és huzal forrasztás alkalmas spray-fémezésre. Amikor a permetezés egy pszeudo dvuhprovolochnye (elektromos ívet vagy gáz-láng) tápláljuk fémszőróban két különböző vezetékek, miáltal egy szórt réteg egy finoman diszpergált keveréke a két leválasztott anyagok különleges tulajdonságokkal, mint például az acél, bronz, acél, molibdén, alumínium-cink és hasonlók. D.
A fémezéshez használt huzal legyen sima, korrodálatlan, tiszta, ütközés nélkül; azt tekercsekre kell tekerni. fémek és fém-oxidok porok legyen száraz és szabadon folyó (túl finom részecskék - kevesebb, mint 10 um - ronthatja folyóképességét, nagy - nagyobb, mint 200 mikron - nem olvasztható kellőképpen).
A műanyagoknak keskeny lágyító területük legyen, függőleges és ferde felületeken nem lehetnek csíkok, a szemcseméretek nem haladhatják meg bizonyos határértékeket.
Mivel a műanyagok permetezésének költsége magas, használata csak akkor ajánlott, ha a színezés nem elegendő. Figyelembe kell azonban venni, hogy a gázláng-metallizáció esetében a műanyag rövid ideig tartó túlterhelést tapasztal, ennek következtében az öntött anyag optimális tulajdonságai nem érhetők el.
A táblázatban feltüntetetteken túl epoxigyanták, polimetakrilát, poliuretán, polisztirol, polimono-klór-trifluor-etilén, polipropilén és bitumen permetezéshez.
7.4. A SPRAY METALIZÁCIÓ TECHNOLÓGIÁJA
Amikor termikus permetezéssel kell alaposan ellenálljon a kívánt folyamat, meghatározzuk amelyek közül: a távolság a bevonandó felületet, teljesítmény és beállító-gun, porlasztás anyag, a tisztaság a sűrített levegő, a permetezési szög, az idő közötti lerakódása az egyes rétegek, termék hőmérséklet és a szórt réteg, mozgó fémszőróban . Más paraméterek másodlagos fontosságúak.
Teljesítmény fémszőróban függ a huzal átmérője, a nyomás a fűtőgáz és az oxigén, valamint a jelenlegi ereje és az anyagot. A változó felviteli körülmények, mint például a típusa és nyomása a porlasztó gázláng beállító (a semleges erősen oxidáló), a távolság a bevonandó felülethez képest (30 450 mm-es), előmelegítése a termék (akár 200 ° C felett), az egyik és a ugyanabból az anyagból lehet permetezni, így réteg különböző keménységű, adhéziós szilárdság, zsugorodási stressz, szerkezet, sűrűség, porozitás, és a különböző megmunkálhatóságot.
A fúvókától a bevonandó felületig terjedő távolság általában 80-200 mm. Hideg fémezés, amikor szükséges, hogy megakadályozza előfordulásának termikus feszültség, valamint a bevonat a papír, karton, fa, szövet, műanyag, üveg és porcelán, ez a távolság növekszik, hogy 200-400 mm. Hot fémezés elvégezni, amikor a felület közötti távolság kell fedezni fémszőróban és 50-től 80 mm-biztosít nagyobb szilárdsága tapadást a szórt réteg, hogy az alapfém, kisebb anyagveszteséggel, de valamivel csökken a keménység (például acél 105 Cr4 már lehetséges elfordulását fogantyú). A távolság az elektroarchikus fémezésnél körülbelül 25 mm.
Nagy porlasztási hatékonyság mellett egyidejűleg megnövelik a permetezett réteg erősségét, mivel a sputtered részecskék hegesztésének valószínűsége nő.
A láng beállításának semlegesnek kell lennie, hogy megakadályozza a porlasztott részecskék oxidációját. Az oxidált részecskék csökkentik az alkalmazott réteg szilárdságát és kopásállóságát (a sárgaréz és a molibdén kivételével, amelyeket 50% vagy 10% felesleg oxigénnel permeteznek).
A permetezett anyagot a lehető legkisebbre kell permetezni, különösen a korrózióvédő rétegekre. Ha drótdarabokat fognak a bevonórétegbe, növelni kell az olvadáspont és a levegőellátó fúvóka közötti távolságot.
A sűrített levegőt le kell üríteni, és nem tartalmazhat olajokat, különben a bevonat eltávolítható.
A permetezési szög általában 90 °, a kerekítésnél 45 ° -os, míg az ujjak belső felületeinek fémezésére - több mint 45 °. Ha több réteg egymást követően kerül alkalmazásra, az alkalmazás közti időnek a lehető legkisebbnek kell lennie, hogy megakadályozza a réteg oxidációját és a por lerakódását (ha ez megtörténik, akkor a bevonat lehúzható). Ha az egyes rétegek alkalmazása közötti szüneteket nem lehet elkerülni, akkor a felületet újra fel kell készíteni.
Annak érdekében, hogy megakadályozzuk a túl nagy feszültségeket az alkalmazott rétegben és ezáltal elkerüljük a repedés veszélyét, a fémesítő réteg hőmérséklete általában nem haladja meg a 100 ° C-ot. Kivételek olyan esetek, porlasztással belső felületei csövek, hüvelyek, csapágyak, hogy elkerüljék zsugorodás igénybevételt, amely javasoljuk előmelegítő és körülbelül 200 ° C-on Permetezés az előbevonat réteg molibdén, nikkel, nikelalyuminievogo ötvözet, alumínium, acél is végrehajtjuk, hogy felületén a előmelegítés 200 ° C-on
A formázott részek szórásával fémezve, a negatív modellt 400-600 ° C-ra hevítik, hogy biztosítsák a negatív forma és a permetezett réteg egységes zsugorodását.
A fémszerkezet mozgásának sebességét úgy kell megválasztani, hogy a rétegvastagság mindegyik átmenetnél kb. 50 μm legyen (például a tengelyek esetében ez a fordulatszám 2-6 mm fordulatonként 10-40 mm per -1 sebességgel).
Az erőssége a bevonatrétegben fokozható a megfelelő előkészítése a védett felület, például vágással egy rongyos menettel és robbantási, az alapozó felhordása alréteg a permetező huzal MiK8 vagy Ni98 (távolság a felület = 30 mm) ív fémszőróban és molibdén - láng-fémszőróban .
7.5. A METALIZÁCIÓS RENDSZER TULAJDONSÁGAI
7.5.1. KARBANTARTÁS
A fémezésréteg az alapfémhez való csatlakozása részben az adhézió, hegesztés, mechanikus kötés és zsugorodás következménye.
A lehúzási szilárdság (merőleges a fémesítő réteg felületére) eddig csak a felületképzés robbantással történt. A táblázatban. A 7.5 ábra bemutatja a permetezett és alapanyagok fő kombinációinak néhány jellemzőjét. Az acélon lerakódott rétegek szilárdsága elektromos íves fémezéssel szinte mindig nagyobb a gázláng-metallizátorok használatához képest.
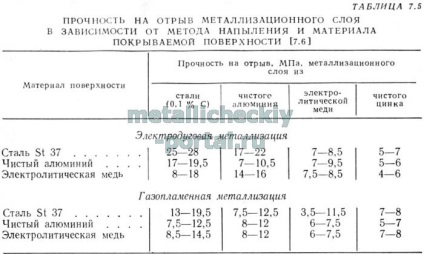
A hegesztett illesztésekkel összehasonlítva a fémezõ rétegek (5 és 30 MPa) hûtõssége nagyon alacsony. Plazma fémezés lehetővé teszi, hogy a magasabb szilárdsági értékek, például a permetezés során rá acél - 80, alumínium, volfrám, molibdén acélból - mintegy 45, 03 A12 acélból egy közbenső réteg NiCr80.20 - körülbelül 65 MPa. A műanyagok esetében a hámozási szilárdság 8-13 MPa. A puha polivinil-klorid héj-szilárdsága 18-26 N cm-1 lehet.
a nyírási tapadási szilárdság (nyírófeszültséget a permetezés síkban) erősen függ az alkalmazás módja és az érdessége a fémezés. Elkészítésekor a bevont felület robbantási adhéziós nyírószilárdság jelentősen nőtt növekvő érdességi mélysége (mélysége 4 mm 10 MPa, 16 m - 35 MPa a felvitt alumínium az acél elektromos galvanizáló).
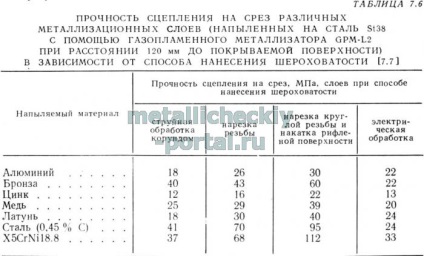
Amikor felület előkészítése kezelést egy sugárhajtású legalkalmasabb érdességi mélysége körülbelül 18 m a vágási szál szakadt - 70-100 mikron.
7.5.2. A BREAK, A RELATÍV KITERJESZTÉS ÉS A LASSANDÁS IDEIGLENES ELLENÁLLÁSA
A metallizációs rétegek áttöréséig tartó átmeneti ellenállása jóval alacsonyabb, mint a sodrott huzal időállósága. A réteg felületére merőlegesen húzódó, az idő ellenállása 5-10-szer kevesebb, mint az időellenállás a réteg mentén. Ez az érték az íves módszerrel alkalmazott rétegek esetében magasabb, mint a gázlángos metallizáció által elhelyezett rétegek esetében. A viszonylagos szakadási nyúlás nagyon kicsi, a zsugorodás általában kisebb, mint az öntött anyagé (7.7. Táblázat).
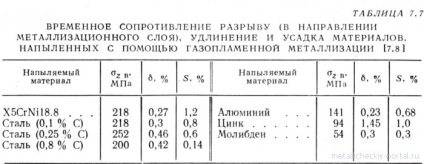
7.5.3. A TÚRÁS MEGHATÁROZÁSA
A fémesítő rétegek nyomószilárdsága magas (pl. Öntött alumínium esetén 120 MPa, permetezett - 220 MPa). Azonban ezek a rétegek nem ellenállnak a nagy lineáris terhelésnek, például gördülő súrlódásnak az általuk okozott eltérítésnek köszönhetően, ami a roncsolódott rétegtől megszakad az alapfémtől.
A keménységmérések bizonyos nehézségeket okoznak, mivel az eredményt erősen befolyásolja a réteg egyedi alkotórészei (például az acélszerkezet edzett, az oxidok és pórusok). Az acélok keménységére vonatkozó adatokat a táblázat tartalmazza. 7.1, porok - táblázatban. 7.3. A HV10 ón bronz keménysége 800-900 MPa, sárgaréz - 750-850 MPa.
A fémrétegek különösen alkalmasak csúszó csapágyakhoz, amelyek nem lehetnek elegendően kenhetőek. Mivel ezeknek a rétegeknek a porozitása 10-15%, jó csaphatóságuk van a csapágyakban és a csúszó súrlódású vezetékekben.
Kavitációs terheléseknél a mikropórusokat tartalmazó fémes rétegek látszólag kevéssé használhatók. Azonban nem végeztek megfelelő vizsgálatokat.
A fémezéssel alkalmazott kerámia rétegek kiváló kopásállóságot mutatnak a szintetikus szálakkal szemben és az acél mentén csúsztatva. A fémezésrétegek kopásának adatai a munkában találhatók.