Koksz és kokszolás
A koksz egy szürke, enyhén ezüstös, porózus és nagyon szilárd anyag, több mint 96% -ban szénből áll, és szénből vagy petróleumkamrákból áll, levegő nélkül 950-1050 ° C-on. A kokszot a természetes üzemanyagok feldolgozásának eredményeképpen kokszolásnak nevezik.
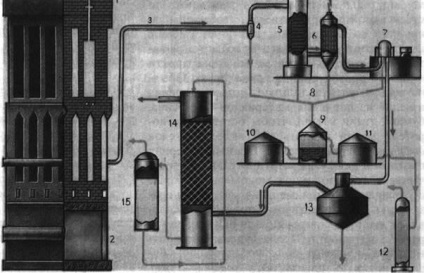
A kokszolás rendszere: 1. - kokszáras elem; 2. - égéstermékek gyűjtőcsatornája; 3. - gázvezeték; - kondenzátum leválasztó; 5. - gázhűtő; 6. - elektrosztatikus felszívó; 7. - gázfújás; 8. - a kondenzátum leeresztésére szolgáló vezeték; 9. - ülepítő tartály; 10. - gyanta tárolása; 11. - ammónia víz tárolása; 12. - ammónium-oszlop; 13. - telítettítő; 14. benzolos mosógép; 15. benzoloszlop.
A kokszot elektrodák készítéséhez használják, folyadékok szűrésére, és ami a legfontosabb, a vasércből és koncentrátumokból származó vasból a vasaló olvasztási folyamatában. A nagyolvasztó kemencében a koksz égése és a szén-monoxid (IV) képződik:
amely kölcsönhatásba lép a vörös-forró koksszel a (II) szén-monoxid képződésével:
A szénmonoxid (II) vascsökkentő, vas oxid (III) -oxid először keletkezik, majd vas-oxid (II) és végül vas:
Ennek eredményeként, a nagyolvasztó folyamat nyert folyadék vas-ötvözet öntöttvas ötvözet, Co-gazdaságban a vasérc és rock-szén koksz, - szén, szilícium, mar-Ganz, foszfor és a kén.
A kokszolás a XVIII. Századból származott. amikor az erdők faanyag előállításához használt, a zselé olvadása során felhasznált fák veszélytelenné váltak, és ezt a szenet más üzemanyagokkal kellett helyettesíteni. 1735-ben Angliában az első kokszkeverő kazán olvasztása történt.
Napjainkban a világ kivont szénének 10% -át kokszká alakítják át. A kokszolást a kokszolókamrákban hajtják végre, amelyeket külső égésgázzal melegítenek. A szén hőmérsékletének növekedésével különböző folyamatok fordulnak elő. 250 ° C-on a víz elpárolog, CO és CO2 felszabadul; 350 ° C-on a szén lágyul, tenyésztő, műanyag állapotba, szénhidrogén-gáz-szelek és alacsony forráspontú szénhidrogének, valamint nitrogén- és foszforvegyületekké alakul ki. A nehéz sárga színű maradékokat 500 ° C-on szinterezzük, így fél kokót adunk. És 700 ° C-nál magasabb hőmérsékleten a félkoksz eltávolítja a maradék illékony anyagokat, elsősorban hidrogént, és kokszká alakul.
Minden illékony termék belép a gázkollektorba, és a megmaradt vörös forró kokszot egy úgynevezett kipattintható edénybe öntik, ahol vízzel vagy inert gázzal lehűtik. Illékony anyagok kondenzációs formában ammónium-víz és gyanta. A nem kondenzálható gáz egy részét a kemencének a kemencék kamrába történő melegítésére használják; a megmaradt gáz, ammónia víz és gyanta feldolgozásra kerül. Különböző szervetlen és szerves (főleg aromás) vegyületeket állítanak elő. 1 tonna szénből körülbelül 800 kg koksz, 150 kg gáz és 50 kg egyéb termék kerül előállításra.
Az aromás szénhidrogének ipari előállításának egyik fontos forrása az olajjal való feldolgozás mellett a kokszszén is.
A kokszolási eljárás elvégezhető a laboratóriumban. Ha a szén erősen felmelegszik egy vascsövön, levegő nélkül, akkor egy idő után lehetőség lesz megfigyelni a gázok és gőzök kibocsátását. Az U-alakú csőben egy kellemetlen szagú gyanta kondenzálódik és fölötte ammóniát tartalmazó víz. További gázokat gyűjtünk egy víz feletti edényben. A kísérlet után a koksz a vascsőben marad. Az összegyűjtött gáz jól ég, úgynevezett kokszkemencék.
Így a szén levegő nélkül történő fűtése során négy fő termék képződik: koksz, kőszénkátrány, ammóniavíz, kokszológáz.
A kokszkémiai termelés alapvetően sok a kokszolók laboratóriumi tapasztalatával, úgy tűnik, hogy nagymértékben reprodukálja.
Ha a szén levegőhöz való hozzáférése nélkül fűtött, a 900-1050 ° C-ig a termikus bomláshoz illékony termékek és szilárd maradék koksz képződéséhez vezet.
A kokszolási eljárás körülbelül 14 óráig tart. A készítés után a képződött koksz "kokszos süteményt" a kamrából kihajtják a kocsiba, majd vízzel vagy inert gázzal leállítják; egy új szénkészlet kerül be a kamrába, és a kokszolási folyamat újra elkezdődik. A kokszszén egy szakaszos eljárás. Főbb termékek: koksz 96-98% szén; kokszolókemence-gáz 60% hidrogén, 25% metán, 7% szén-oxid (II) és más melléktermékek. szénkátrány (benzol, toluol), ammónia (gáz a koksz), és mások.
Lehűlés után a koksz válogatásra kerül, és a kohászati kemencékhez szállítják.
Az illékony termékeket a kamrák tetején levő nyílásokon keresztül ürítik ki, és belépnek egy közös gáztartályba, ahol - tapasztalataink szerint - gyanta és ammónia víz kondenzálódik.
Az ammónia és a könnyű aromás szénhidrogének (elsősorban a benzol) nem kondenzálható gázból származnak. Az ammónia kivonása céljából a gázt kénsav oldatán keresztül vezetjük át; A kapott ammónium-szulfátot nitrogén-műtrágyaként használják.
Az aromás szénhidrátokat oldószerrel való abszorpcióval és a kapott oldatból származó desztillációval nyerik.
A kőszénkátrányból frakcionálással benzol, fenol (karbonsav), naftalin és mások homológjait kapjuk.
A tisztítás után a kokszolt gázt az ipari kemencékben tüzelőanyagként használják, mivel számos éghető anyagot tartalmaz. Kémiai nyersanyagként is használják. Például a hidrogént a kokszolókemencéből különféle szintézissel szabadítják fel.
A szénhidrogén nyersanyagok felhasználásának problémái:
Egészen a közelmúltig az ország olajkitermelése óriási mennyiségű olajat tartalmazott. Az energiaellátás fejlesztésével kapcsolatban az olaj és a kőolajtermékek tüzelőanyagként történő felhasználását széles körben használják a földgáz, a szén és az atomenergia felhasználásának céljára. Ez azt jelenti, hogy az olaj-mazut feldolgozás során keletkező nehéz maradványokat jobban feldolgozzák könnyűolajtermékekké, amelyek a modern szerves szintézishez szükségesek. A kémiai tudománynak az a feladata, hogy hatékonyabb módokat találjon az olaj, a természetes és a hozzá kapcsolódó gázok feldolgozására, a szénre, a palántákra és a meglévők tökéletesítésére annak érdekében, hogy a természetes szénhidrogén-nyersanyagokat jobban és átfogóan felhasználhassák.
A mesterséges fűtőolaj beszerzése nem új probléma. A szén-hidrogénező üzemet 1923-ban vezették be Németországba, 1943-ban Németország 2 millió tonna benzint és 800 000 tonna dízel üzemanyagot kapott. A mesterséges folyékony tüzelőanyagok előállításának folyamata nagyon drága volt, és 70 MPa nyomáson és 180 ° C hőmérsékleten végezték. A háború utáni években a szén hidrogénezése gyakorlatilag elvesztette ipari jelentőségét.
Jelenleg a tudósok a gazdaságilag előnyösebb szénhidrogénezési módszereket fejlesztik hatékony katalizátorok alkalmazásával, ami lehetővé teszi a hőmérséklet és a nyomás csökkentését.
A szintetikus folyékony üzemanyag megszerzésének másik ígéretes módja a szénmonoxid (II) és a hidrogén szintézise.