A koncepció a „just in time» (just-in-time, JIT)
Az egyik legelterjedtebb a világon a logisztikai koncepciók a koncepció a Just-in-time -JIT (just in time). A megjelenése ezen fogalom arra utal, hogy a végén a 1950-es évek, amikor a japán cég a Toyota Motors, majd más autógyártók japán cégek elkezdték aktívan végrehajtja Kanban rendszer.
A kezdeti koncepció volt a jelszó JIT kivételével potenciális készleteket anyagok, alkatrészek és félkész termékek a gyártási folyamat az összeszerelés autók és a fő egység. A kezdeti probléma úgy néz ki, mint ez: ha meg a gyártási ütemtervet, meg kell szervezni a mozgás anyagáramlás, hogy az összes anyagok, alkatrészek és félkész termékek kapott a megfelelő mennyiségben, a megfelelő helyen (egy futószalagon), és pontosan a kijelölt időben a gyártása vagy összeszerelése a késztermék. Ebben a készítményben a probléma több biztosítási tartalékok befagyasztása az alapok a cég, felesleges.
Elvileg a JIT -Alkalmasság szolgált alapul a későbbi végrehajtásának logisztikai koncepciók / technológiák, mint a Lean Production, ( «lapos” vagy »vékony« termelés) és a hozzáadott érték logisztika - «Logisztikai hozzáadott értéket képvisel.”
Ez izolálni és jellemezni alapgondolata az eljárás, amely három feltételezésre épül (amely empirikusan megerősítést többször helyes).
Először is, azt feltételezzük, hogy a fogyasztók igényeit a kész termékeknek meg kell felelniük az nem előre felhalmozott tartalékokat és a termelési kapacitás, készen arra, hogy a feldolgozott alapanyagok kapott szinte „kerekekkel.” Ennek eredményeként, a készletek volumenének, minősülő fagyasztott kapacitás minimalizálható.
Másodszor, tekintve a kötelező tartalék szükséges folyamatos racionalizálása szervezése és irányítása a termelés, a nagy mennyiségű készletszintek, abban az értelemben, elfedi a hibákat és hiányosságokat ezen a területen, a szűk helyen a termelés, nem szinkronizált működés, a kihasználatlan termelési kapacitás, megbízhatatlan munka A szállítók és viszonteladók .
Harmadszor, hogy értékelje a hatékonyságát a termelési folyamat, amellett, hogy a költség- és teljesítmény alapok figyelembe kell venniük az időszak a javaslat, az úgynevezett teljes hossza a termelési ciklus. Rövid végrehajtásának feltételeit javaslatok megkönnyítik a menedzsment a vállalat, és hozzájárul a versenyképesség növekedését azzal a képességgel, hogy gyorsan és rugalmasan reagálni a külső körülmények változását.
Ellentétben a hagyományos módszerekkel a beadás, amely szerint a központi eleme a termelés tervezési kérdésekről gyártási megrendeléseket minden osztályon és ipari egységek, a módszer a „just in time” központi tervezés kizárólag az utolsó láncszem a logisztikai lánc t. E. A késztermék raktár. Az összes többi termelési és ellátási egység kap megrendeléseket közvetlenül egy másik található, közel a vége a logisztikai láncszem. Például egy raktár késztermékek adott alkalmazás (ami egyenértékű a kibocsátás termelési feladat) bizonyos termékek száma aulájában, szerelőcsarnok elrendeli a gyártás részegységek feldolgozás üzletek és áruházak együttműködés és t. D.
Ez azt jelenti, hogy a termelési cél mindig kimeneti egység, amely (vagy folyamat) ezt a részletet. Ezáltal anyagáramlás a „forrás”, hogy egy „fogyasztó” megelőzi egy információáramlás fordított irányban, vagyis a termelés "just in time" előzetes tájékoztatás "just in time".
A koncepció lényege az a meggyőződés, hogy a készletek fordulnak elő, mert a rossz gazdálkodás, gyenge koordináció a munka és így a problémák rejtett tartalékok. Arra a következtetésre jutottunk, hogy meg kell találni az oka a különbség a kereslet és kínálat, javítja a teljesítményt műveletek, ami után a készletek el fog tűnni. A koncepció a Just-in-time (Just in Time) vezet szemléletformálás az alábbi területeken:
· A készletek. Szervezeteknek kell azonosítani és megoldani a problémákat, ami a készletek, hajlamos a minimum (nulla leltár) anyagi források, a munka folyamatát és késztermékek.
· Minőségi. Nem szükséges, hogy elérjék egy elfogadható szintre, a házasság, és annak teljes hiánya az integrált minőség-ellenőrzés.
· Szolgáltatók. Az ügyfelek kell támaszkodnia a beszállítóik, így kell, hogy a hosszú távú kapcsolatokat kisszámú megbízható szállítók és hordozók.
· Volume felek. Meg kell keresni a módját, hogy csökkentsék a termelési mennyiség tételekben, hogy elérjék a rövid gyártási ciklusok esetben többletet nem halmozódik fel a késztermékek készleteit.
· Átfutási idő. Meg kell csökkenteni átfutási idő csökkentése érdekében bizonytalanságok, amelyek megváltoztathatják a helyzetet sokáig a szállítás.
· Megbízhatóság. Minden műveletet kell elvégezni folyamatosan, megszakítás nélkül, azaz nem kell bontást, házasság, a hiányzások, stb
· Az alkalmazottak. Szüksége van az együttműködés szellemében, mind a dolgozók és a vezetők között és a dolgozók, mint hogy minden attól függ, hogy a teljes siker a munkában, mind a munkavállalók egyenlő módon kell kezelni, a tisztességes bánásmód. Felbátorodva bármilyen kreatív kezdeményezés által kifejezett bármely alkalmazottja az esetleges javításokat a munkában.
· Információs támogatás lehetővé teszi a gyors információcserét, és szinkronizálja a folyamatok az ellátási anyagi források, gyártása és szerelése, a kínálat a késztermékek.
Így JIT - nem csak egy módja annak, hogy minimálisra csökkentsék a leltár, hanem hogy megszüntesse a mindenfajta hulladék az erőforrások, javítja a koordinációt és a hatékonyságot.
Az egyik első kísérlet gyakorlati megvalósítása JIT koncepció éppen időben vált a fejlett társasági Toyota Motors rendszer KANBAN (japánul - „kártya”). Kanban rendszer az első „húzza» JIC munkahelyi amelynek végrehajtása a cég által Toyota megkezdte fejlődését vett körülbelül 10 év. Egy ilyen hosszú ideig annak a ténynek köszönhető, hogy a nagyon Kanban rendszer nem tudott dolgozni anélkül, hogy megfelelő logisztikai környezetben.
A legfontosabb elemei a környezet voltak:
· Rational szervezet a termelés és az egyensúly;
· Egy átfogó minőségirányítás minden szakaszában a gyártási folyamat és a minőség nyersanyagforrások beszállítóktól;
· Partnerség megbízható beszállítói és hordozók;
· Javítják a szakmai felelősség és a magas munkaerkölcs a személyzet.
Kanban rendszer. úttörője a Toyota Motors Corporation 1972-ben a növény „Takahama” (Nagoya), ez egy szervezeti rendszer folyamatos termelés, amely lehetővé teszi, hogy gyorsan változik a termelés és nem igényel külön biztosítási állományok. A lényege a KANBAN rendszer lényege, hogy minden termelési egység az üzem, beleértve a végső futószalagon szállított az anyagi források csak a mennyiség és az ilyen kifejezés, ami szükséges a megbízás, sdelannnogo osztály fogyasztókkal. Így, ellentétben a hagyományos megközelítés a szerkezeti egység gyártója nem rendelkezik általános kemény operatív menetrend termelés és optimalizálja a munkát annak érdekében kötet, miután a vállalat termelési és technológiai részleg ciklust.
Micrologistical KANBAN rendszer által generált futószalag-termelés, de annak elveit lehet alkalmazni az egész ellátási lánc és bármely típusú termelés. Kanban a „húzó” olyan rendszer, amely ellenőrzi a kereslet a legtöbb „helyes” pont a logisztikai lánc.
A fő cél -, hogy csak a szükséges mennyiségű termelési szerint a kereslet végén vagy egy közbenső (következő) a fogyasztót. Például, ha a komponens szükséges a futószalagon, azok el vannak látva az előző termelési oldalon a lánc a megfelelő mennyiségben és időben, amikor szükség van rájuk. És így tovább az egész logisztikai termelési láncban.
Kanban rendszer jelentősen csökkenti az állomány anyagi források a bejáratnál és félkész termékeket az aljzatból, így azonosítani „szűk” a gyártási folyamat során. A vezetés irányítja a figyelmet, hogy ezek a „szűk”, hogy foglalkozzon a legjövedelmezőbb módon. Amikor a problémát sikerült megoldani, A puffer térfogatát készletek csökkentek újra, amíg nincs nyoma a „szűk keresztmetszet”. Így Kanban rendszer lehetővé teszi, hogy az egyensúlyt az ellátási lánc minimalizálásával készletek minden szakaszában. A végső cél - az „optimális egyik fél által.”
Eszközei információtovábbítás a rendszer egy speciális KANBAN kártya egy műanyag borítékot. Közös a két típusú kártyák: a kiválasztás és a termelés érdekében. A kártya kiválasztását jelzi az alkatrészek számát (komponensek, félkész termék), amelyet be kell venni az előző feldolgozási rész (összeszerelés), mivel a gyártási sorrendben a kártya - az alkatrészek számát, amelyek kell gyártani (összeszerelve) az előző termelési hely. Ezek a kártyák forgalomban mind a vállalatok Toyota, valamint a társasági és kölcsönhatásba lépnek a cégek, valamint a bankfiókban vállalkozások. Így KANBAN kártyák információt hordoznak fogyóeszközök és gyártott mennyiséget.
Fontos eleme a Kanban rendszer az információs támogatást, beleértve nemcsak a kártyákat, hanem a termelési, szállítási és ellátási grafikus grafikus kártya technológia, az információs eredményjelző, stb.; szabályozási rendszer igényeit és a szakmai személyzet forgás; integrált rendszer (TQM) és szelektív ( "Jidoka") minőségellenőrzési; A rendszer összehangolása a termelés és számos más.
Végrehajtása Kanban rendszer. majd annak módosított változata lehetővé teszi, hogy:
1. jelentősen javítja a termék minőségét;
2. hosszának csökkentése logisztikai ciklus, jelentősen növelve ezzel a forgalmat a működő tőke társaságok;
3. csökkenti a termelési költségeket;
4. gyakorlatilag megszünteti a biztosítási állomány, és jelentősen csökkenti a befejezetlen készletek.
Elemzés élményt alkalmazási rendszer KANBAN számos ismert műszaki cégek azt mutatja, hogy ez lehetővé teszi, hogy csökkentsék a készletek 50% áru - 8% egy jelentős gyorsulást forgalomban működő tőke és minőségének javítása, a késztermék.
Példa a rendszer működésének KANBAN
A diagram azt mutatja, két megmunkáló központ (OC): OO1 részének felhasználásával A gyártásához félkész B és OTS2 segítségével félkész termék gyártására a C. Mindenekelőtt meg kell dönteni, hogy milyen típusú tartály, amelyet fel kell használni minden helyzetben, B C, és a méretük, azaz hány egység minden egyes termék elfér egy tartályban.
A rendszerben nincs helyszíni tároló tartályok át az egyik a másikba OC segítségével technológiai eszközökkel.
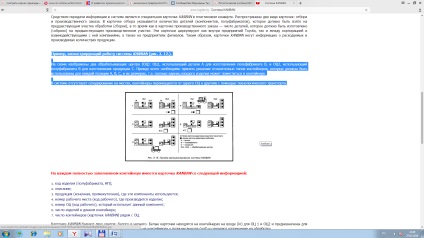
Minden teljesen megtöltött tartályt egy KANBAN kártyát a következő információkat:
1. A termék kód (a félig-NP);
3. termékek (végső, közbenső termék), ahol ezeket a komponenseket alkalmazzák;
4. A számú munkahelyi (üzemi kód), ahol a terméket előállították;
5. szoba OC (munka) kód, amely használja a hatóanyagot;
6. A tételek száma a tartályban
7. A konténerek száma (KANBAN kártyák) közelében OT.
KANBAN kártyák két színben: fehér és fekete. Fehér lap a konténerek a belépő (a) az OZ 1 és OTS2 és szállítandó. Fekete KANBAN lap a konténerek a kilépési helyzet (ki), valamint olyan engedély feldolgozás.
Az információ a kártyákat, hogy kapcsolódnak a konténerek, utal egy különleges tartályban.
Black Card tételek C a kimenete az üres tartály. Ebben az esetben azt jelzi megoldás OTS2 (dolgozik a központban), hogy a termék, mint egységek C megtöltéséhez szükséges egy üres tartályba. Ehhez OTS2 használ egy konténer részletesen, ahol voltak tárolva OTS2 bemeneti és felszabadítja a fehér kártya KANBAN (2. reakcióvázlat).
Ez a kártya engedélyezi a szállítás egy másik tartály elemeit a OO1 (kilépési) a OTS2 bemenet. A munka a teherautó az újonnan mentes tartályt és egy fehér kártya jön OO1, amely eltávolítja a fekete kártya teli tartályt a részleteket, és hagyja mellett az üres tartályt, és a fehér kártya, hogy rögzítse a tartály tele van a részleteket, és továbbítja azt OTS2. Szabad fekete kártya ahhoz, hogy a termelés OO1 következő teli tartály részei B. A folyamat során a tartály gyártási felszabadul a terméket A, és egy fehér kártya jelzéseként szolgál a szállító utánpótlási alkatrészeket egy konténer, stb
A fenti példa - egy tipikus rendszer „húzza” a növény logisztikai rendszer, ahol a konténerek az alkatrészek (komponensek gyártási készletek) mozog csak a fogyasztási adatokat a későbbi részekben.
Fontos eleme a Kanban rendszer az információs támogatást, beleértve nemcsak a kártyákat, hanem a termelési, szállítási és ellátási grafikus grafikus kártya technológia, az információs eredményjelző, stb.; szabályozási rendszer igényeit és a szakmai személyzet forgás; integrált rendszer (TQM) és szelektív ( "Jidoka") minőségellenőrzési; A rendszer összehangolása a termelés és számos más.